Finanzielle Bestandsaufnahme der Produktionsanlagen
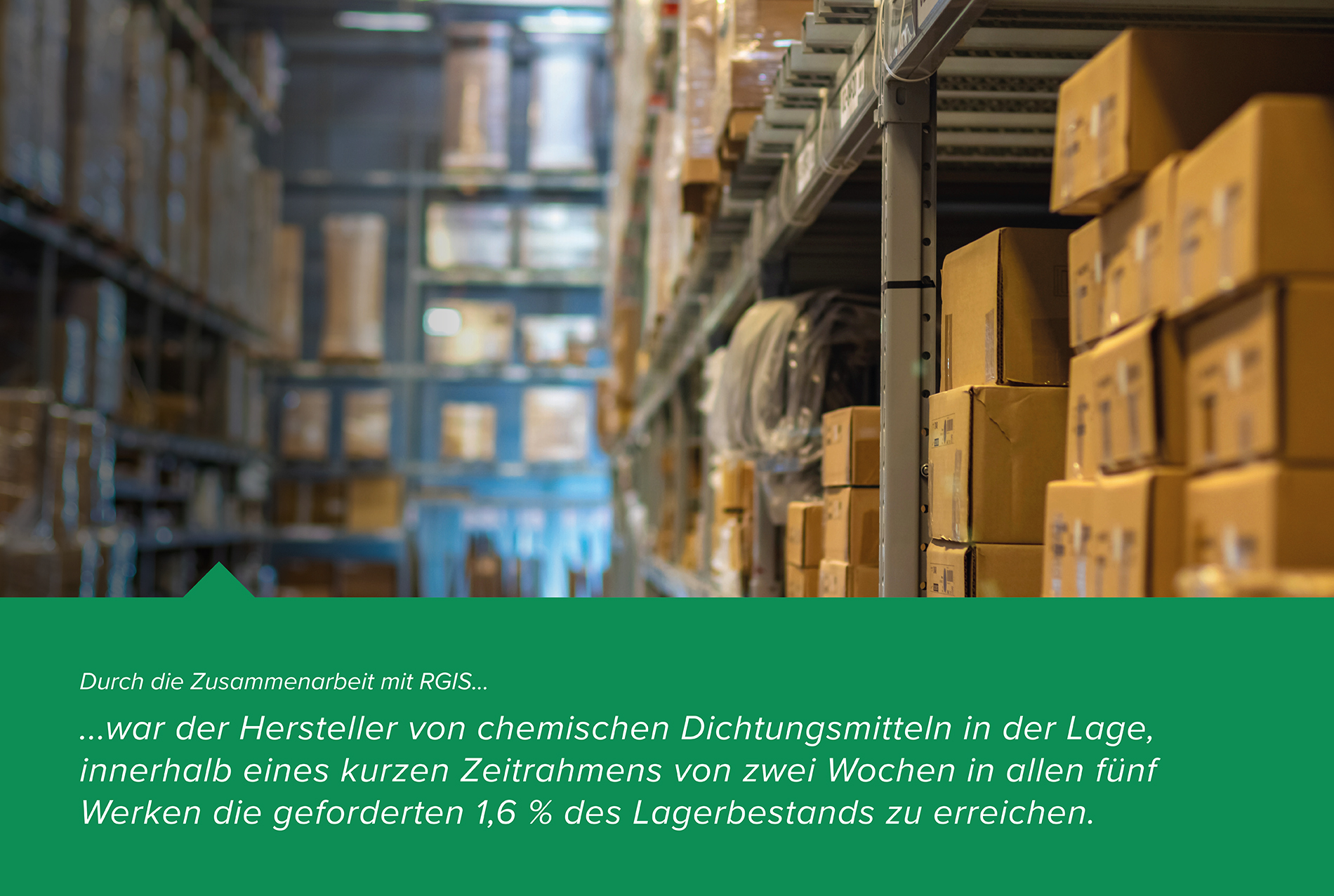
Ein 1937 gegründeter Hersteller von chemischen Spezialdichtstoffen benötigte die Unterstützung von RGIS. Seit seinen Anfängen ist das Unternehmen kontinuierlich gewachsen, indem es das Angebot an chemischen und mechanischen Produkten, zur Unterstützung der Handwerker bei ihrer Arbeit, erweitert hat.
ANFORDERUNG
Der Hersteller von chemischen Dichtungsmitteln benötigte eine Lösung für eine finanzielle Bestandsaufnahme von fünf Anlagen in fünf Bundesstaaten am selben Tag, ohne die Produktion während der Woche unterbrechen zu müssen, um weiterhin Anlagen zu kaufen. Der Hersteller verlangte von RGIS die folgenden Leistungen:
- Nationale Abdeckung seitens RGIS, um die erwarteten fünf Staaten abdecken zu können
- Alle fünf Einrichtungen müssen innerhalb eines kurzen Zeitraums von zwei Wochen zur gleichen Zeit gezählt werden
- Abweichungen müssen identifiziert werden
- Jede Einrichtung muss innerhalb von 1,6 % der gesamten Bestandsdatei liegen
LÖSUNG
Der Hersteller von chemischen Dichtungsmitteln hat sich mit RGIS zusammengetan, um das Projekt “Finanzielle Bestandsaufnahme der Produktionsanlagen” abzuschließen, und hat die folgenden Angaben gemacht:
- Ein Team von 400 erfahrenen RGIS-Auditoren wurde zusammengestellt, die eng mit dem internen Team zusammenarbeiteten
- Aufgrund des engen Zeitrahmens für die Durchführung der Inventur organisierte RGIS die Anmietung von Scherenhubwagen sowie die Schulung und Zertifizierung von über 70 RGIS-Teammitgliedern
- Identifizierung von Etikettierungsproblemen, die zu zusätzlichen Abweichungen führen könnten
- Zählen der SKU (Stock Keeping Unit) und der Menge
- Erfassen und Analysieren aller Daten, um Abweichungen korrigieren zu können
- Sicherstellen, dass keine Paletten übersehen wurden, da die Paletten doppelt tief gelagert wurden
ERGEBNISSE
Der Hersteller von chemischen Dichtungsmitteln hat durch die Auslagerung des Projekts zur finanziellen Bestandsaufnahme der Produktionsanlagen an RGIS, die folgenden Ergebnisse erzielt:
- Bestehende Prozesse in den Einrichtungen des Verkäufers, mit denen die Käufer nicht vertraut waren:
- Etikettierungs-, Herstellungs- und Kundendienstprobleme, z. B. dass der Kunde nicht das richtige Teil erhält
- Systemprobleme, bei denen der Lagerbestand in Dollar für das Produkt in der Produktion mit dem Lagerbestand in Dollar für das Rohmaterial übereinstimmte, ohne dass der Arbeitsaufwand berücksichtigt wurde
- Fehlen eines Etikettierungssystems und Bestandseinlagerungsprozessen
- Es wurde festgestellt, dass die SKU-Etikettierung im Produktionsbereich nicht übereinstimmte
- 10 % der Produkte waren nicht im System erfasst – sobald der Artikel vom Lager in die Produktion verschoben wurde, änderte er seinen Namen und wurde mit einem anderen Namen zurück ins Lager gelegt
- 30 % der Produkte hatten einen anderen Barcode als die angegebene Beschreibung
- 15% des Lagers enthielten gemischte SKUs und Standorte
- Es wurde ein Anstieg der Bestände festgestellt – etwa 1,1 % bei 20 Millionen Dollar
- Es wurde ein sechs Jahre altes Inventar identifiziert, das der Verkäufer in den Büchern hatte, von dem der Käufer aber nichts wusste